4/17/24
Long gap in posting due to working other jobs and lack of time to spend on LDM printer.
As a result, this week when I decided to get it going again, I took apart the extrusion head and realized I had not cleaned it properly to leave it idle. :-/
Unscrewing the printed plastic portion from the stepping motor portion I found that the auger screw was stuck in the plastic housing. With some fuss I was able to remove the plastic portion but in doing so I stretched the aluminum spring that connects the auger to the motor.
I’m replacing this piece, called…“5mm to 6mm Shaft Coupling 25mm Length 18mm Diameter Aluminum Alloy Coupler”
I actually ended up changing this again, as the auger side did not need the 6mm diameter, and in hopes to keep everything even more on axis I bought a similar coupler…
“5mm to 5mm Shaft Coupling 25mm Length 18mm Diameter Aluminum Alloy Coupler”
and also replacing the bearing that lives on the screw below the coupler…
“6mm Bore ID, 19mm OD, 6mm Width Pre-Lubricated High Speed Sealed Miniature Bearings”
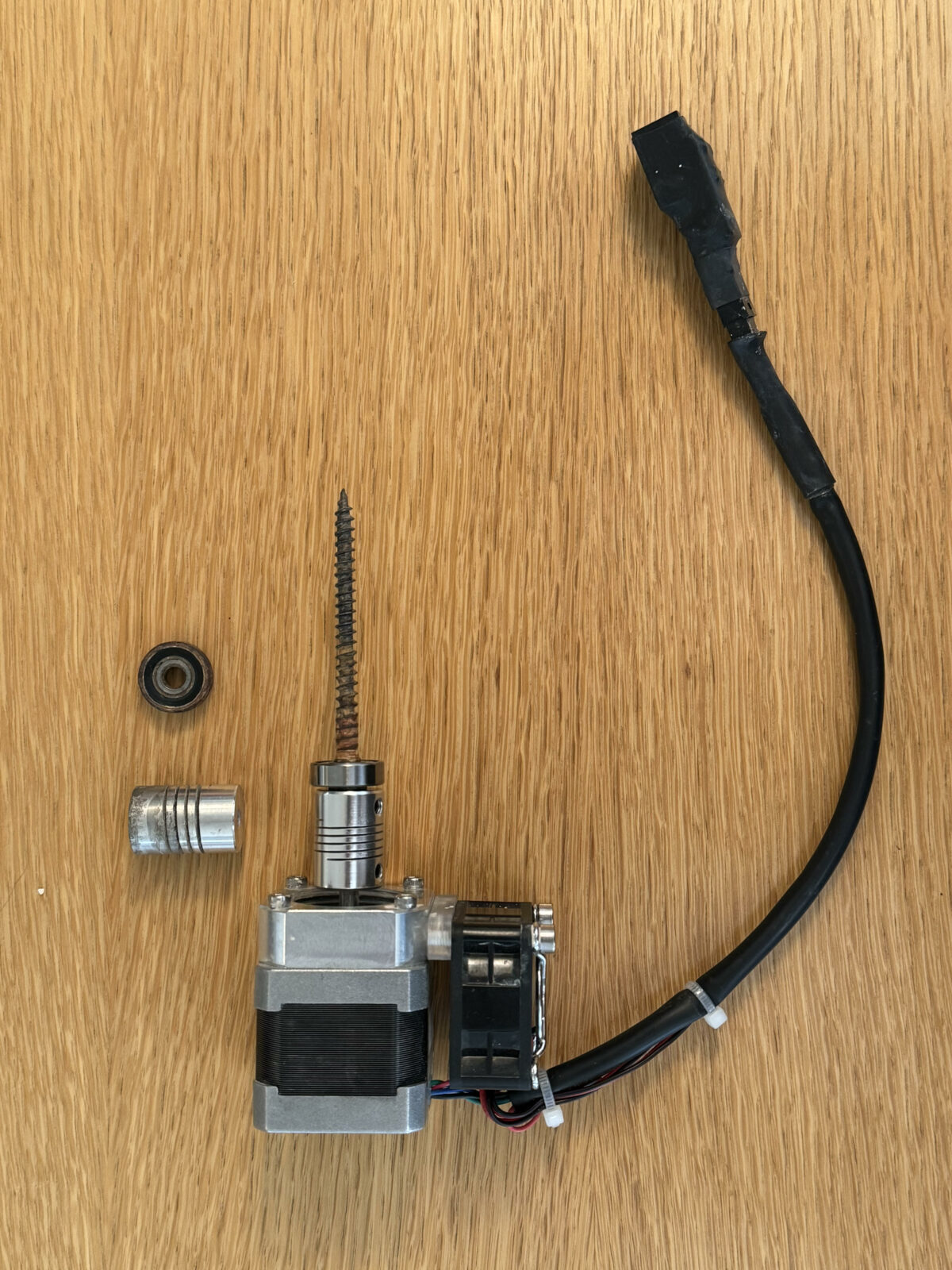